CNC PILOT 640 contouring control
Program complex tasks with ease
- 24 control loops (22 with functional safety), including up to 6 spindles
- Multi-touch screen
- Up to 3 channels for asynchronous multi-slide machining
- Programming: smart.Turn, G codes, or cycles
- Extensive machining and probing cycle packages
- 5-axis simultaneous machining
- Fast block processing time (1.5 ms)
- TURN PLUS: program at the push of a button
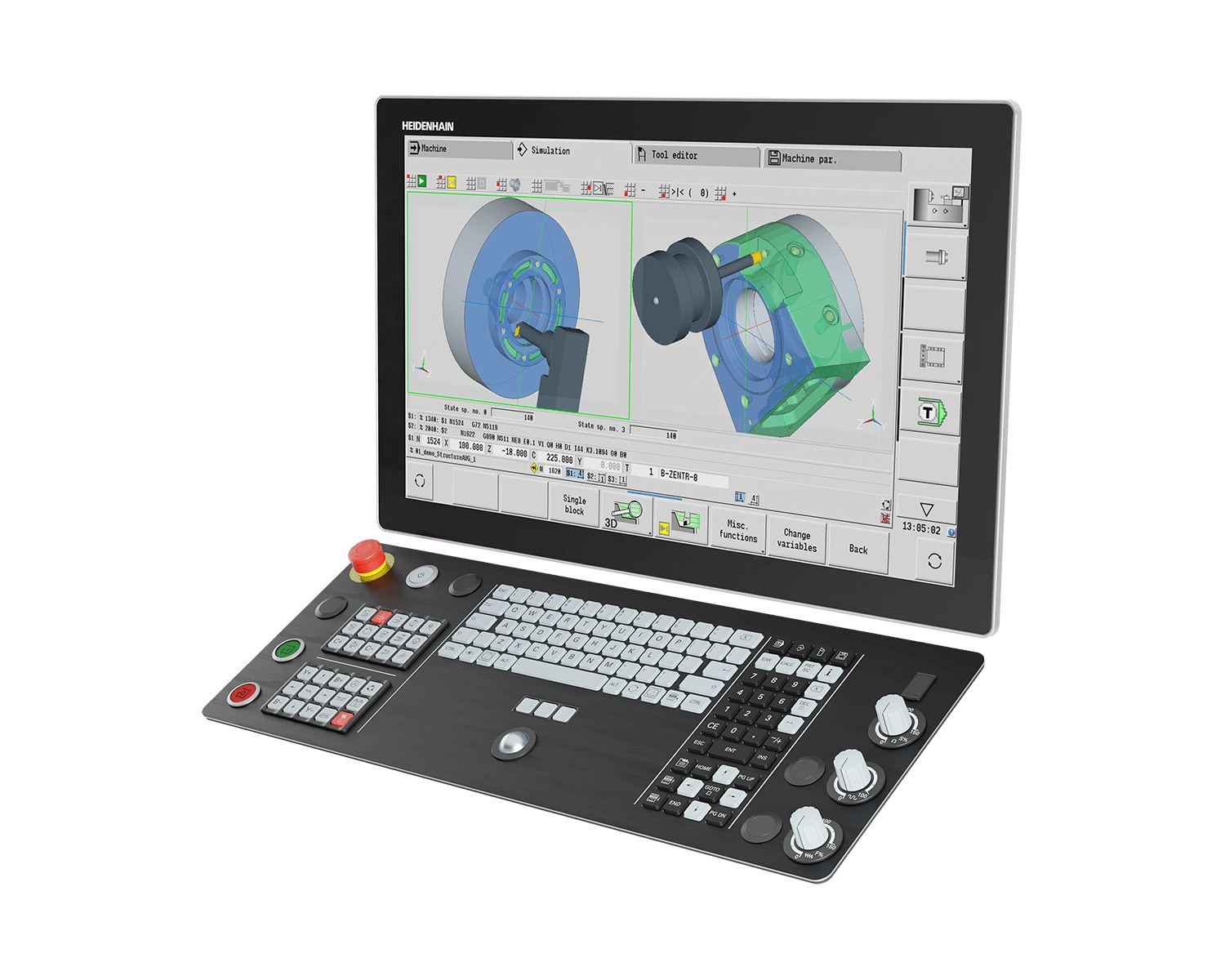
Application diversity
Whether for counter spindles, driven tools, or C, Y, and B axes, the CNC PILOT offers numerous convenient and high-performing functions. Multi-channel machining even makes it possible to perform various machining steps with multiple slides at the same time.
Automatic programming
The TURN PLUS automatic programming function is the fastest route from a design drawing to the finished workpiece. After the contours of the workpiece blank and finished part have been entered, all that remains is to select the material and workholding equipment. TURN PLUS automatically takes care of the rest at the push of a button.
Structured programming
Programming is particularly easy thanks to smart.Turn functionality. All parameters are illustrated by context-sensitive support images and entered in forms. The program’s machining blocks are well structured and easy to read.
Handy machining cycles
The CNC PILOT 640 is equipped with an extensive range of cycles. Cycles for turning, milling, and drilling are standard features. Convenient cycle programming is even possible for complex operations such as multiple plunging, simultaneous machining, trochoidal milling, and hobbing.
Complete machining
The complete machining of front and rear sides offers enormous benefits: higher accuracy, fewer errors, shorter run times, and lower costs per part. Programming this is easy thanks to smart functions such as spindle synchronization, traversing to a fixed top, and controlled parting.
Load Monitoring
The Load Monitoring option monitors spindle and motor loads on the machine, continuously comparing them with load values from a reference operation. As a result, the CNC PILOT 640 immediately detects tool breakage or wear, triggering a predefined reaction.
Application-oriented design
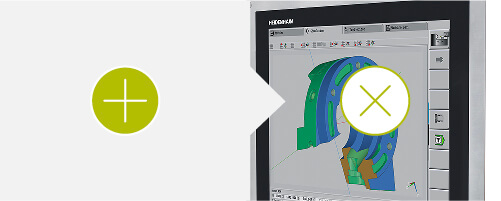
Click the plus signs to learn more about the product.
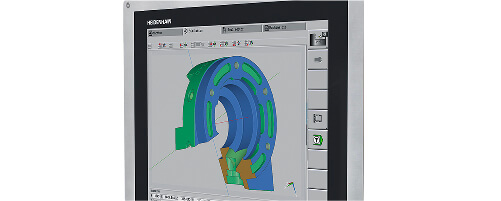
Gesture control makes it very easy to zoom and rotate simulation graphics as well as to navigate through programs, tables, or menus
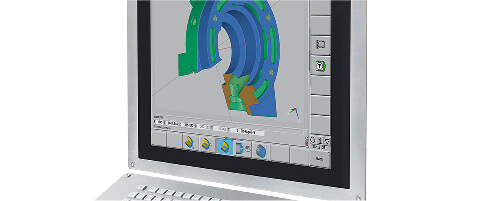
The intuitive and clearly structured user interface make simple operation and optimal orientation possible
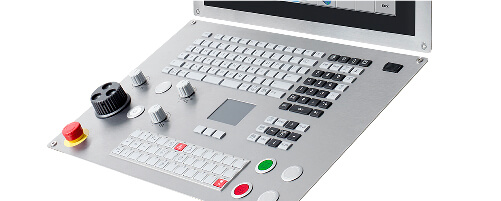
The well-structured operating panel is systematically divided into function groups and features meaningful key symbols
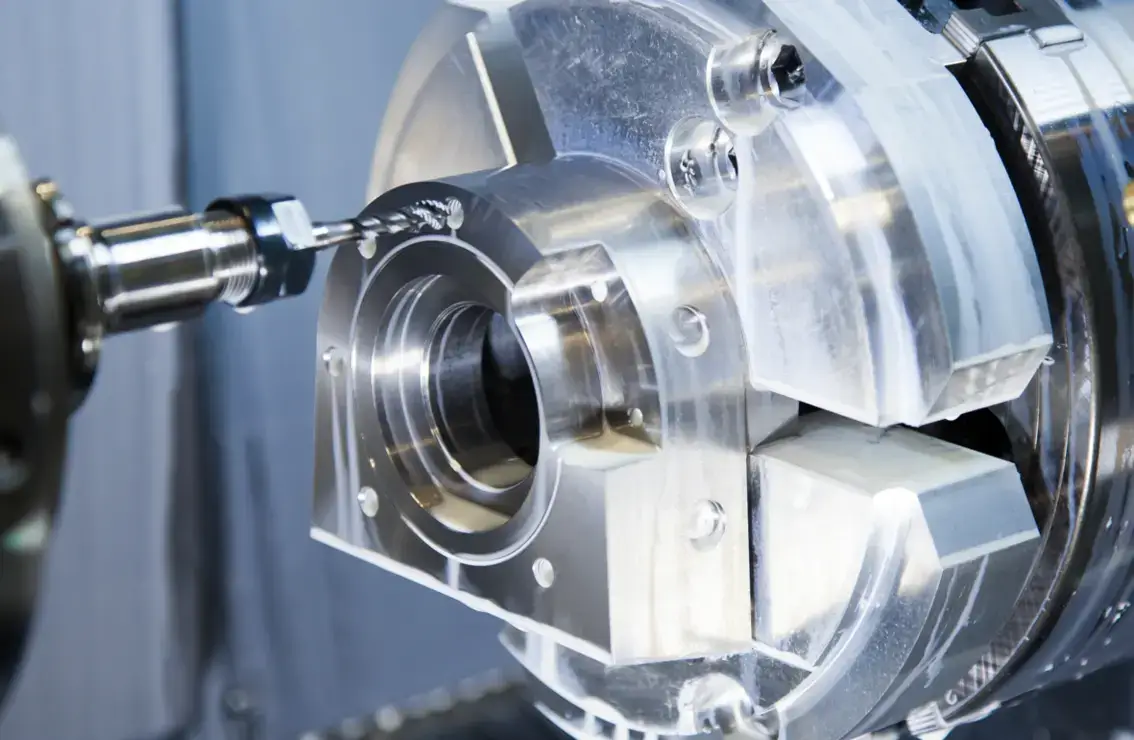
High-end turning
Thanks to its wide range of programming capabilities, the CNC PILOT 640 offers the right support for simple to complex parts in single to serial quantites. Its practical operation requires only minimal training. The CNC PILOT 640 supports lathes with a main spindle, counter spindle, C axis, positionable spindle, and driven spindle, as well as machines with a Y axis and B axis. In multi-channel machining, different machining steps can be performed with multiple slides at the same time.
Easy connectivity
Easy data usage, time-saving workflows, and transparent processes: Connected Machining enables optimal connection to digital job and data management solutions in a manufacturing context. With the Connected Machining package of functions, HEIDENHAIN controls can be perfectly integrated into process chains through future-ready digital interfaces and flexible operating designs, thus optimizing the transfer of knowledge within your company. Connected Machining incorporates HEIDENHAIN controls into the purely digital job management landscape of a production network and places the user at the center of the digital job management process.
Connected Machining delivers:
- Easy data usage
- Time-saving workflows
- Transparent processes
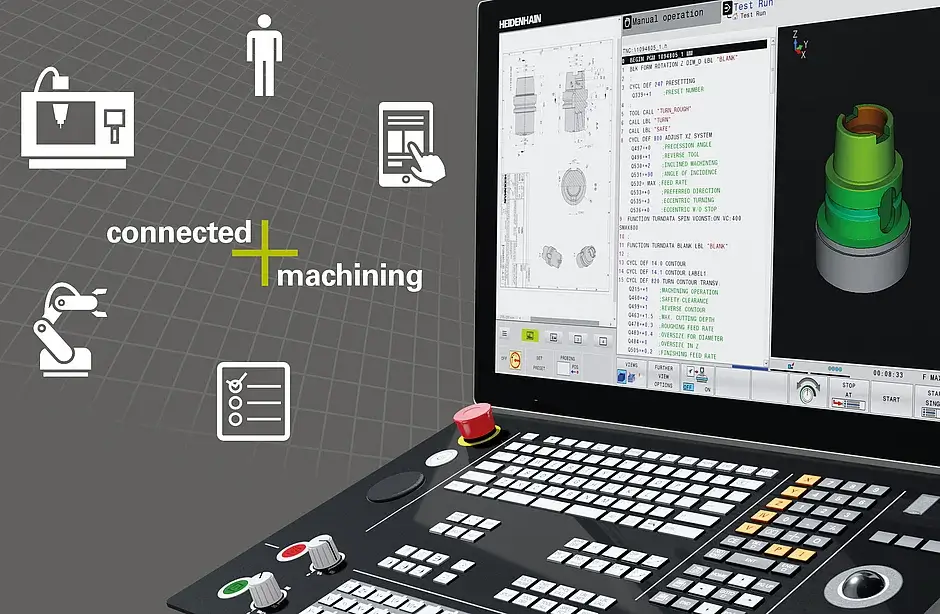
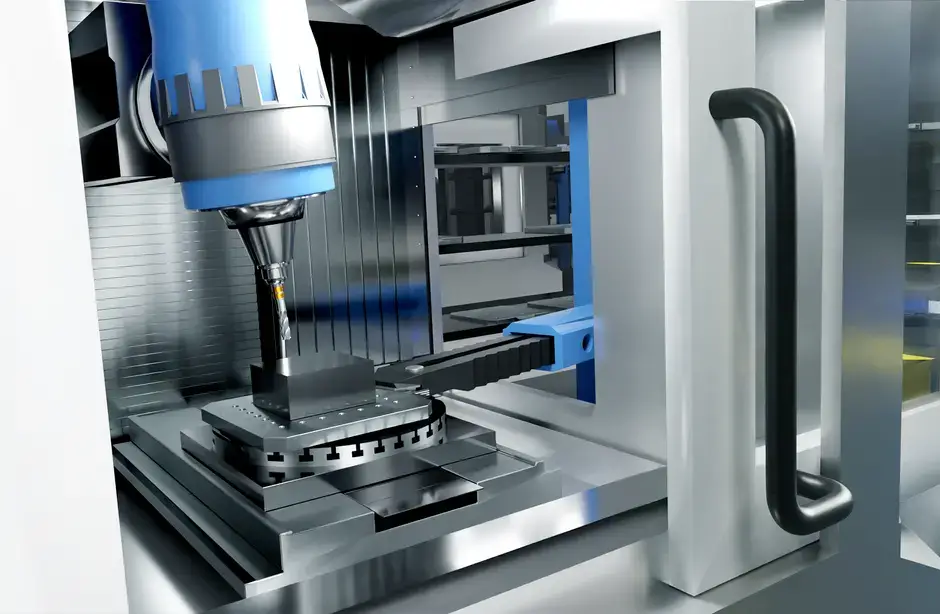
Easy entry into automation
The automation possibilities for machine tools are wide-ranging and depend on a variety of factors. The HEIDENHAIN Automation Solution is an individualized modular package made up of different hardware and software products. The package’s software delivers intuitive operation to users, who can implement seamless tool and workpiece movements without extensive training. Machine manufacturers and automation providers can adapt the user interface to their needs and add their own operating functionality.
The key benefits at a glance:
- Intuitive, easy-to-operate user interface
- Universal data interfaces to all common machine tool controls
- User admin function for preventing improper operation