TNC7 basic contouring control
Compact, intuitive and powerful
- 8 control loops, up to two of which are for spindles
- Highly responsive operation and smooth, intuitive touch operation
- Extensive smart probing and machining cycles
- Graphically guided workpiece and fixture setup
- High surface quality with short machining times
- Fast block-processing time (0.5 ms)
- Successor to the TNC 620
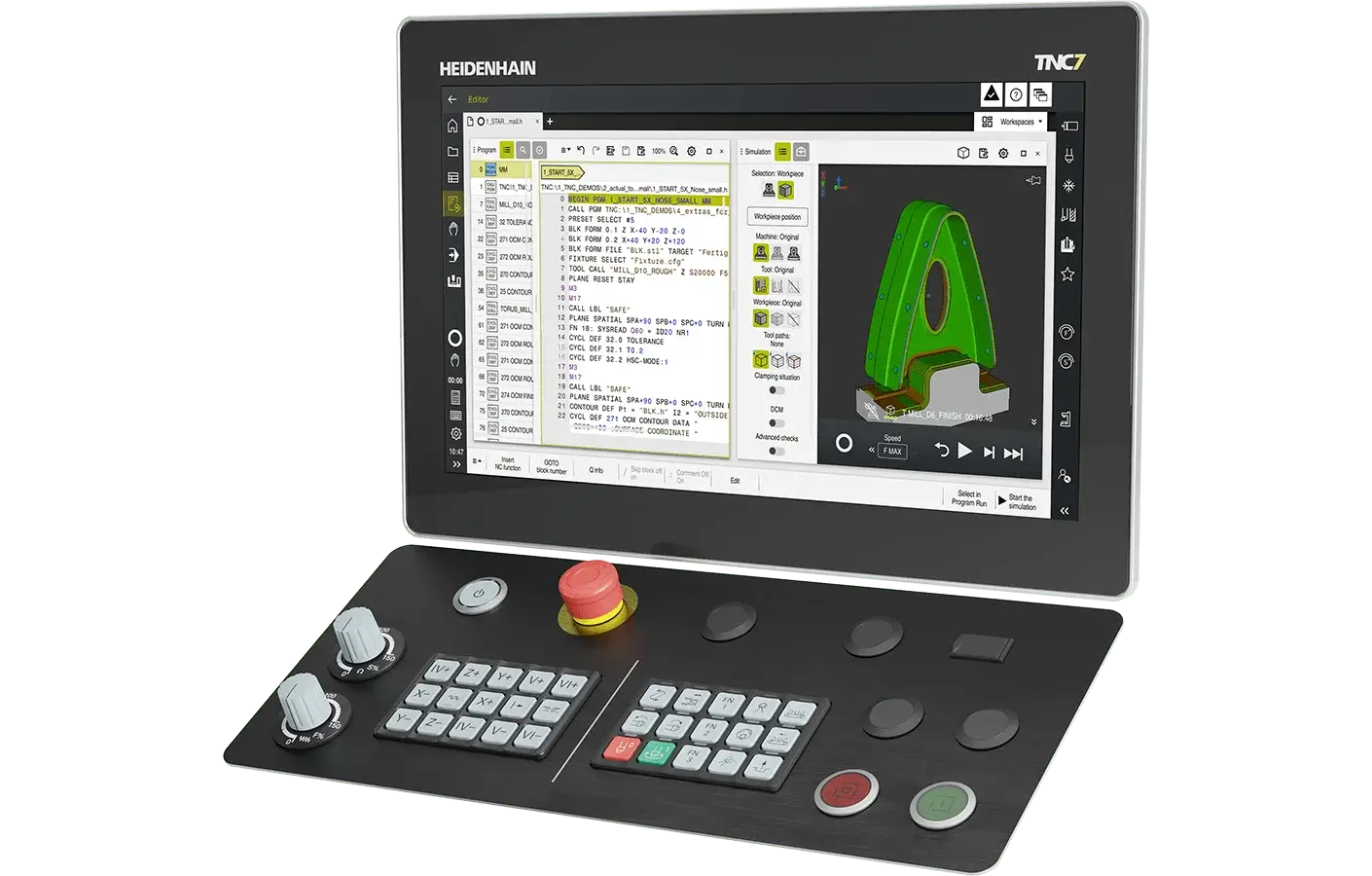
Customizable operating interface
Users of the TNC7 basic enjoy optimal support for whatever their work calls for, including NC progrmaming, machine setup and part inspection. The screen of the TNC7 basic can also be customized, allowing users to arrange functions and information exactly as needed. The control’s Dark Mode enhances user experience in low lighting conditions.
Versatile installation
The TNC7 offers exceptional user-friendliness in a compact form factor. Combinable with a full-size keyboard or a machine operating panel, the TNC7 hardware is adaptable to a variety of machine designs. High-quality components ensure fast responsivness and smooth touch control, contributing to an outstanding user experience.
Optimized motion control
The Advanced Dynamic Prediction (ADP) function provides motion control optimization. ADP dynamically precalculates the contour, adapting the machine’s movements based on a jerk-smoothing acceleration limit. As a result, perfect surfaces are can be attained even with a highly variable point distribution.
Intelligent programming
The TNC7 basic adds smart functions to the familiar HEIDENHAIN Klartex programming language. New graphical programming functionality lets users draw contours directly on the touchscreen. Final contours are translated into and stored as Klartext code. It’s also an easy way to modify existing programs.
Fast and accurate machining
The Dynamic Precision and Dynamic Efficiency software packages provide many high-performance functions for even more efficient and accurate TNC7 machining. They’re a fast and dependable way to achieve perfect parts by applying high-efficiency machining strategies, optimized motion control, jerk reduction and more.
Predictive protection
Protect your machine from damage while preventing downtime. The Dynamic Collision Monitoring (DCM) function monitors the machine envelope across all operating modes and stops machine movements in response to potential crashes. Further protection is provided by targeted component monitoring that detects spindle wear and overload before it’s too late.
Sustainable manufacturing with the TNC7
Software options for 6D setup support allow TNC7 users to probe fixtures and workpieces up to five times faster, thus saving considerable time and energy. Thanks to the non-stop monitoring of components and processes, along with extensive simulation capabilities, the TNC7 increases the process reliability of machine tools.
Practical design
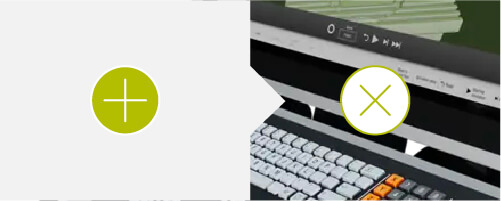
Click the plus signs to learn more about the product.

The touchscreen’s high responsiveness ensures smooth operation through gestures familiar from mobile devices.
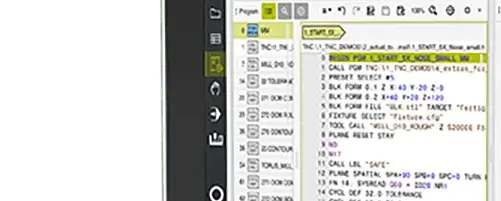
The screen’s workspaces can be adapted to individual needs and wishes. Customization possibilities include status notifications, NC functions, favorites for files, a home menu for a fast start and personalized user management settings.
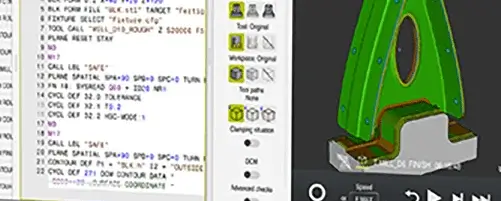
The control offers multiple ways to create NC programs. A new highly intuitive one involves drawing contours directly on the touchscreen. Klartext remains the file and exporting format, thereby allowing the continued use of existing NC programs.
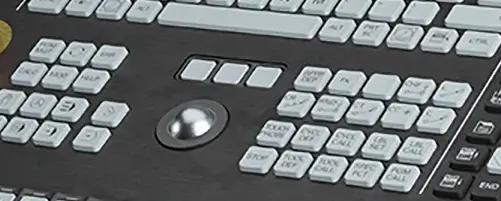
The newly developed keyboard features an improved mechanical design, including optimized key resistance. The improved ergonomics simplify your work and perfectly complement touch operation on the screen.
Graphical programming
The smart way to create NC programs
NC programing is now even faster and easier thanks to the TNC7’s graphical programing feature. This function allows users to work within the part drawing on the touchscreen. The control translates this graphical data into a savable Klartext program. This process also works in reverse: changes made within a Klartext program can be converted into a dimensioned drawing through dragging and dropping.
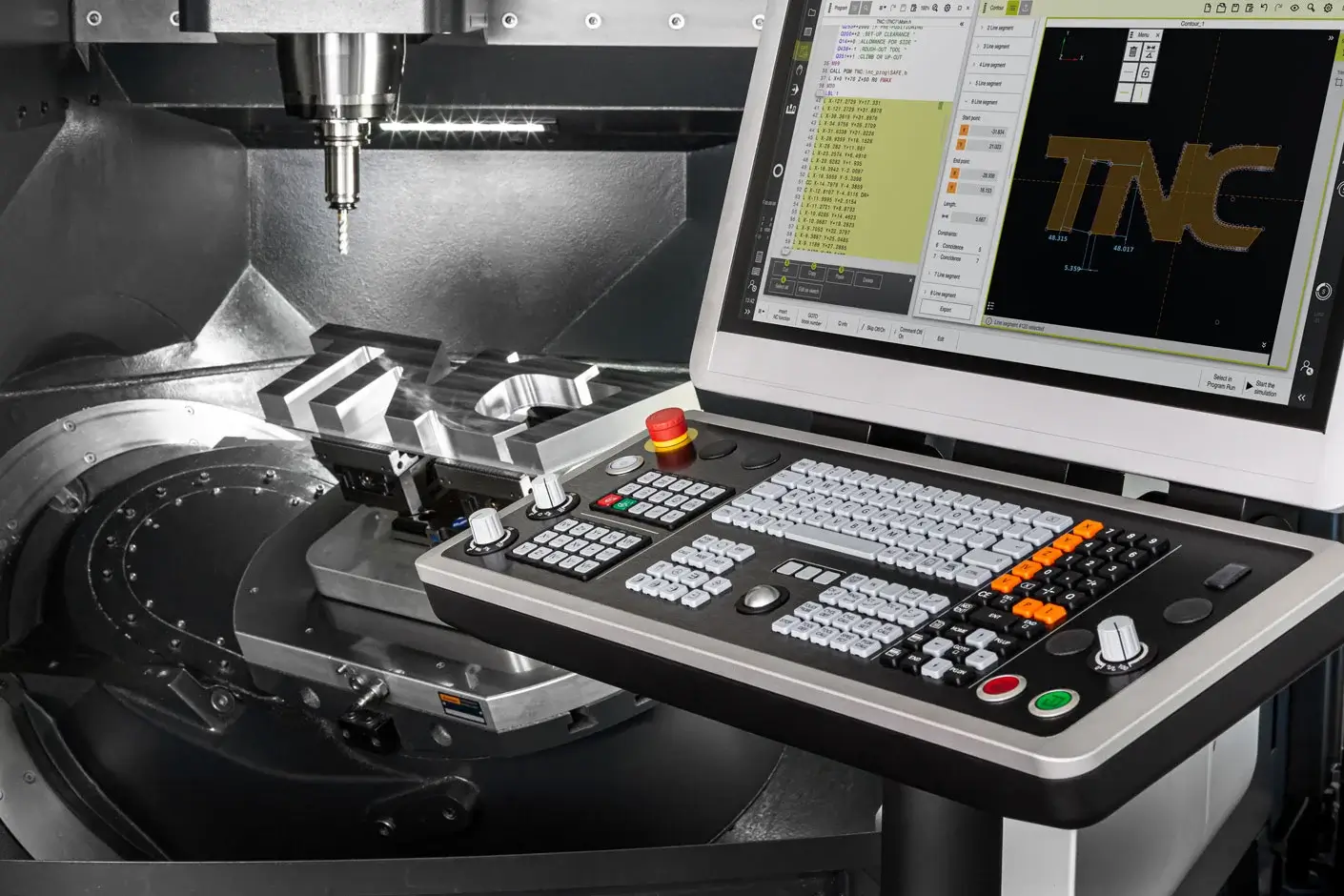
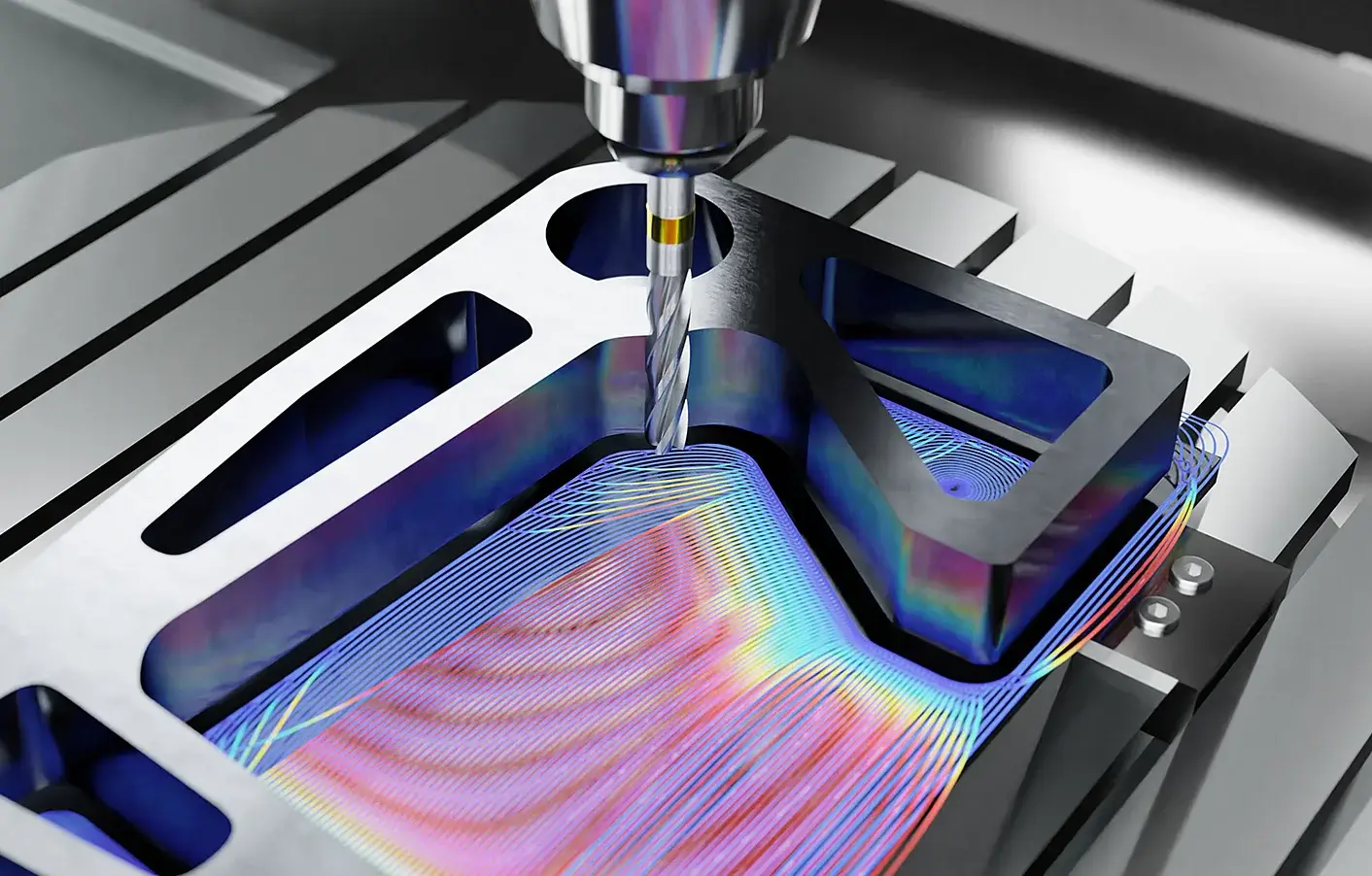
Optimized Contour Milling (OCM)
Always mill with optimal cutting data
Achieve reliable machining under constant cutting conditions and less tool wear with OCM. After users simply input their contours, the control automatically calculates the best trochoidal milling strategy. This functionality applies the benefits of high-efficiency trochoidal milling to a much wider range of parts, enabling more productive millling at low tool wear.
Intuitive machine setup
Enhanced collision protection for fixtures
The TNC7 basic takes Dynamic Collision Monitoring (DCM) to a new level. DCM on the new control not only prevents tools from crashing into machine components but also into fixtures. Users need only a 3D model of the fixture plus the new Collision Monitoring v2 software option. The control interactively guides users through the process of probing and thereby locating the fixture on the mahcine table. Intelligent probing cycles ensure a fast and reliable process. And for workpiece setup, Model Aided Setup (MAS) supports users with graphical guidance throughout workpiece setup in six degrees of freedom.
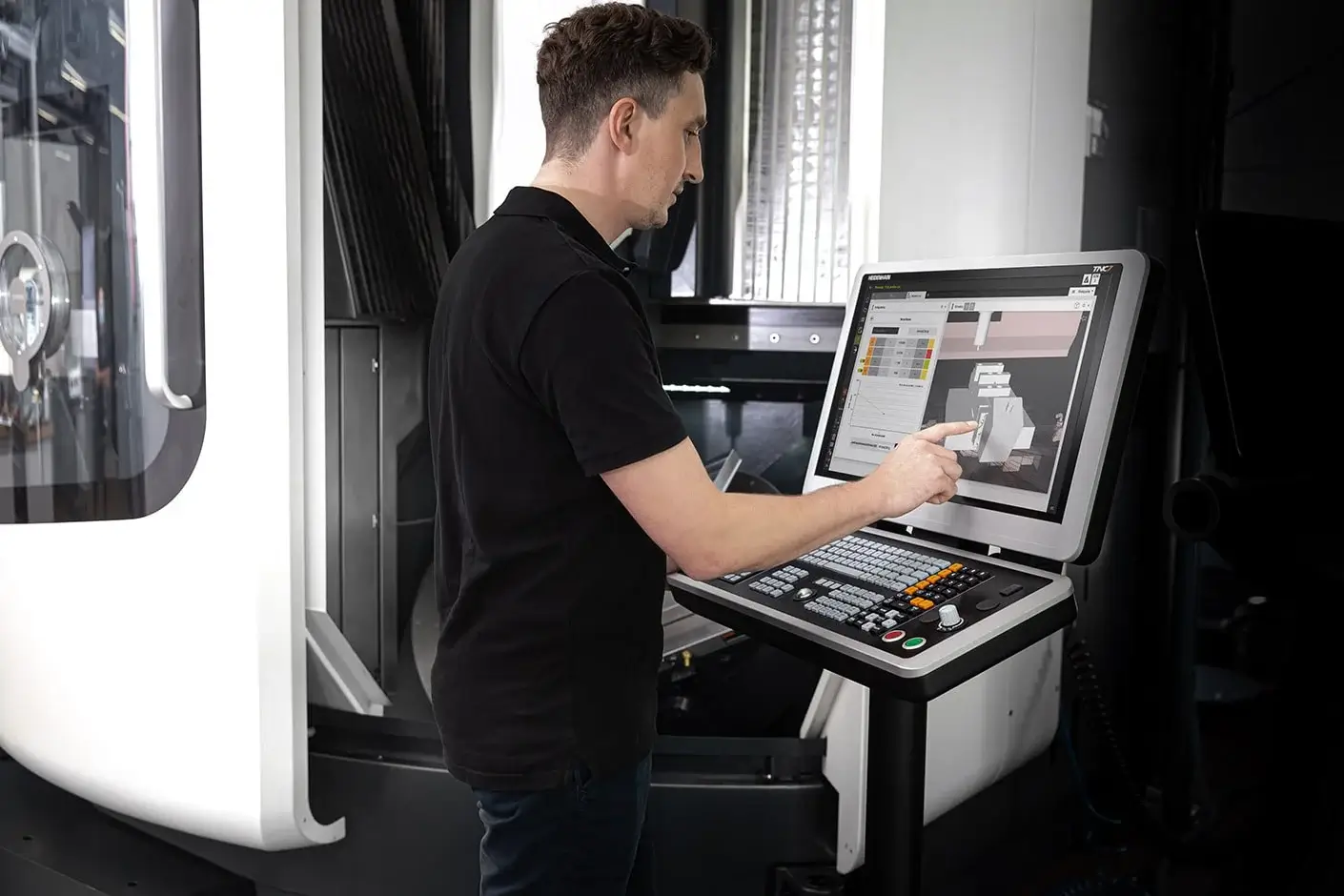
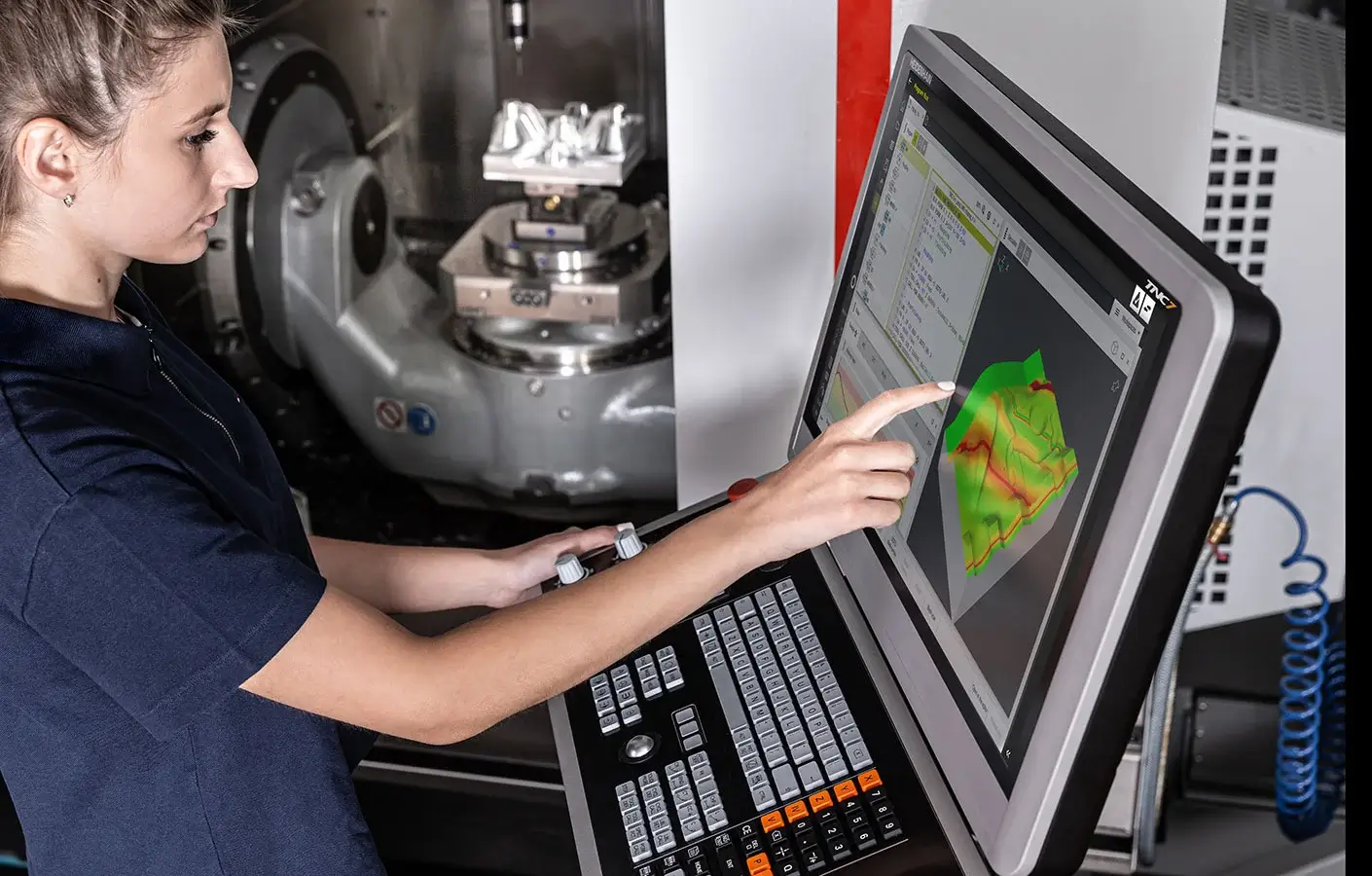
TNC component monitoring
Protect your machine from excessive loading
TNC Component Monitoring is a toolbox for machine manufacturers that allows them to reliably implement extensive monitoring functions in their machines. These functions include real-time process monitoring for preventing severe overloading, and data collection for predicting mechanical wear.