November 5, 2019
How to select a servo motor
- Servo motors are a type of electric motor that allow for precise control and use a closed-loop system with feedback devices.
- Proper selection depends on understanding load requirements and environmental conditions, including torque, speed, efficiency and winding type.
- Environmental factors like contamination, temperature and vibration must also be considered in selection.
- Servo motors are used in a wide range of applications from industrial machinery to everyday mechanisms.
Updated on: 12/20/2019
Servo motors are a type of electric motor (rotary actuator) that allows for precise control of position, velocity and acceleration. They employ a closed-loop system, meaning there’s a feedback device (like an encoder) that communicates with a control such as a CNC machine control.
Magnetism controlled by electricity is used to drive these motors. The number of magnetic poles impacts the characteristics of the motor as a whole: The lower the number of poles the faster it can spin, but the reachable torque will be lower and vice versa. Servo motors use either AC or DC current. With AC, speed is determined by the frequency of voltage, while speed is directly proportional to a DC voltage. Brushed motors use conductive material inside the cylinder slide against the commutator as it rotates. Brushless motors use electricity exclusively. Servo motors can also be solid or hollow shaft.
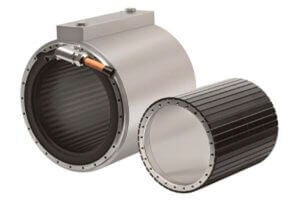
ETEL’s TMB+ Torque Motor with closed cooling jacket
They are used in a wide range of applications from industrial machinery to the everyday mechanisms in buildings or devices. This variety makes understanding how to select a servo motor and grasping the factors to consider when doing so important.
Top three factors in choosing a servo motor
The process of calculating and selecting a servo motor for an application or system is often referred to as sizing. That’s because the most critical formulations, the relationships between speed and torque, of the application essentially determine how big the motor needs to be and its relative force density. To calculate these, application factors like the weight of the payload, distance and speed of the cycle, and rest/cooling between movements need to be established; this is also known as the duty cycle.
Once the application is specified, identifying the peak torque, continuous torque and speed required of the motor will dramatically narrow down which motor is right. Torque and speed go hand in hand when selecting a servo motor. Torque curves are a tool used to represent this relationship, showing when relative torque and speed can be sustained simultaneously, both continuously or intermittently.
Two other useful terms to know about torque in servo motors and the torque curve are rated torque and rated speed. Rated torque is the maximum torque a motor can produce continuously—on the line dividing the continuous and intermittent zones—and rated speed is the top speed that rated torque is available.
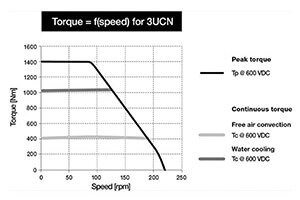
A typical graph of the relationship between torque and speed for a servo motor
Continuous torque
Continuous torque, also known as root mean square (RMS) torque, is a time-weighted average of torque during a complete cycle; this needs to fall in the continuous region of the torque curve to be able to maintain the required speed.
Peak torque
Peak torque is the most torque required at any one point throughout the cycle. Ideally, peak torque is in the intermittent region of the torque curve because it’s not as sustainable. If the peak torque required by the application falls in the motor’s continuous region, it’s likely oversized.
Speed
Just as important as the load’s weight when selecting a servo motor is knowing the speed, typically in RPMs, that will be required. Generally speaking, the higher speed at which a given motor spins, the lower the possible torque. We mentioned poles earlier; a low pole count results in high speed and low torque because of different factors including Back EMF.
The closer the cycle runs to the motor’s limitations, the hotter it will get. A motor needs to be selected that won’t overheat, but also isn’t too big to not be cost effective. Once these relationships are determined, other important, but less mission critical, factors can be established.
Other key factors in choosing the right servo motor
While identifying speed and torque requirements get us most of the way toward identifying the right servo motor, there are other factors and options to consider depending on the environment and application.
Gear ratio
Not all servo motors have gears, but many do. With the advent of direct drive motors, geared motors are considered more primitive, but can be used to amplify torque capabilities of a lower pole count motor. In a geared system, the servo motor turns a driver gear which turns another gear that is more closely connected to the payload. (There can be more than one gear pairing in a servo motor.) The ratios of the number of teeth between the gear pairings formulates the gear ratio. Once this is established, the standard torque equation is used to calculate the real torque of the motor.
Inertia
When dealing with rotation, the payload’s shape and mass generate inertia when the motor and the load accelerate or change direction. The motor has its own inertia in the rotor, which is often negligible compared to the payload, and so does the load, which is increased by any friction in the motion, such as pullies or tables. Inertia can be used when there isn’t a known torque value, as it’s the mass of the F=ma equation when dealing with rotation.
Accuracy
A direct drive motor isn’t mechanically limited in its accuracy, meaning the motor will operate as accurately as the feedback it uses. That said, the encoder is typically selected more based on what fits within the overall mechanical structure rather than a result of the motor performance.
Environment factors
Environmental factors affect the overall selection because if the environment is different than standard room temperature than the motor’s performance changes. For example, the higher the ambient temperature, the lower the continuous torque that’s possible. In a setting where there is high ambient temperature and/or continuous torque requirements, liquid cooling is a good option, but direct contact with the motors mechanics and connection must be avoided.
Other environmental factors include contamination and vibration, which can be common in places like paper mills, oil rigs or steel mills. Motors with specialized, rated, sealing and integration are made specifically for these applications.
Efficiency
The efficiency of a servo motor is simply how much current is needed to achieve a constant torque value. This is referred to as torque constant (Kt) and can be found on a motor’s data sheets.
Windings refer to the different ways in which the coils are wired relative to each other (in series or parallel) and the different winding options give the following tradeoffs: Windings with greater current efficiency have lower speed capabilities, while windings with higher speed capabilities have lower current efficiencies. When the required speed is known then the winding will be based on what’s the more efficient choice while still reaching the required speeds.
Summary
Selecting the right servo motor starts with understanding the application, establishing the characteristics of what’s moving, how it’s moving and how fast. From there, the key speed and torque requirements can be established which will significantly narrow down the motors to choose from. Other factors like environment, efficiency, accuracy and gearing should be considered. Of course, the order and priority of any of these can vary by application.
At ETEL, we choose to offer DC, brushless, synchronous, high-pole-count servo motors. We use a DC power supply to convert AC to DC and synchronous design to offer users more precise control. Brushless motors are more reliable, efficient and less noisy than the brushed alternatives. Along with a high-pole-count, up to four winding options per size allow the motors to deliver the speed often required of today’s automation and production environments.
If you want to take a deeper dive on this, or any other motion control topic, we make our experts available. Schedule a consultation now to start finding specific solutions to your challenges.