June 26, 2017
Increase machine tool accuracy in six axes of movement
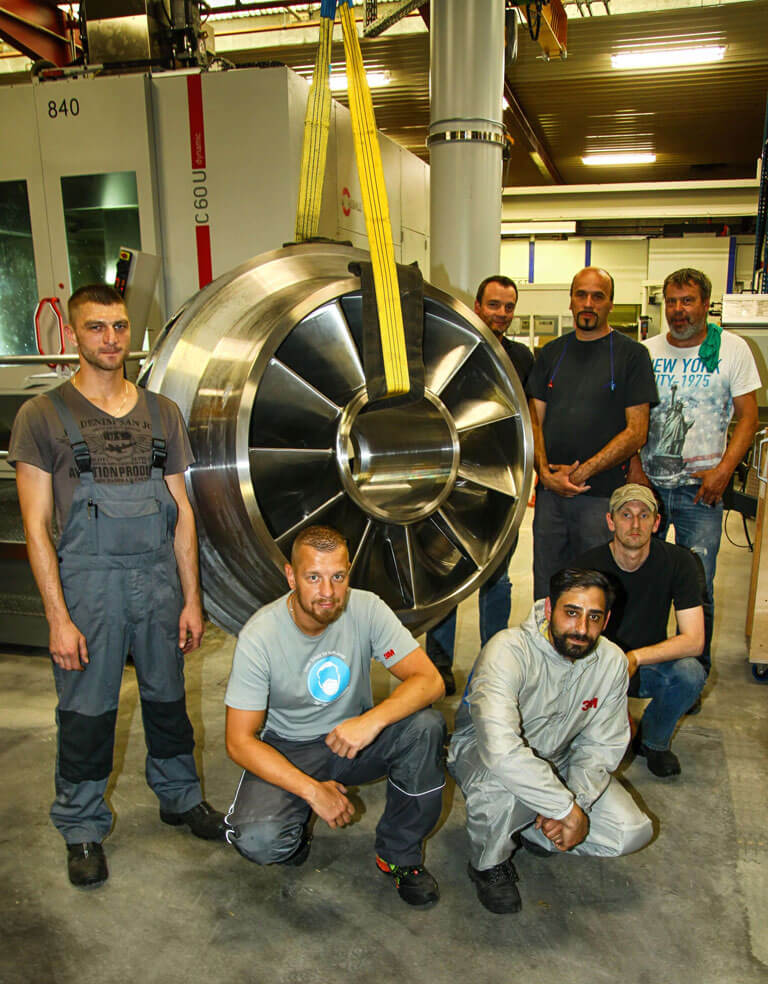
Präwest specializes in manufacturing complex parts.
An innovative measuring method used by a high-tech machining company based in Bremen, Germany (a leader in the field of 5-axis milling of complex parts), helps the company improve the accuracy of its four biggest machine tools.
Präwest Präzisionswerkstätten captures their machine tools’ volumetric errors with Etalon’s LaserTracer-NG and compensates them in HEIDENHAIN’s machine tool control through the software option KinematicsComp. The result: Dimensionally accurate workpieces without any readjustments—even with demanding free-form parts with diameters of up to 2.5 m (98 inches).
Thanks to its focus on innovative production processes and permanent staff training, Bremen-based contract manufacturer Präwest has climbed to the top of the turning and milling market. Customers include big players from the aerospace industry such as MTU, Rolls-Royce, and Mitsubishi Heavy Industries ordering impellers, blisks, turbine shovels, and structural components. Also renowned industrial groups, e.g. MAN, Siemens as well as businesses from the oil and gas sector, appreciate the expertise of the German precision manufacturer.
Specialist for tough geometries, materials, and processes
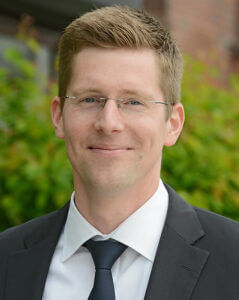
Gaylord Klammt, Head of Business Area Industry at Präwest
Präwest’s product portfolio starts where other turning and milling workshops have to give in: “We solely manufacture parts with complex characteristics,” explicates Gaylord Klammt, Head of Business Area Industry at Präwest. “Everything the market considers as exceptional would be a standard issue for us. One could say: Each project is a box full of surprising challenges.”
The workpieces often show complicated geometries or are extremely big and heavy, not to mention their strain and stress. In addition, customers frequently ask for elaborate additional processing, e.g. chromate coating or heat treatment, even for a batch size of one. Daily business is also the processing of difficult-to-machine materials such as the superalloy Inconel 718 that contains a high percentage of nickel (50%). The manufacturing complexity becomes apparent, too, when looking at the number of required tools: “To turn a single workpiece to the desired shape and dimensions, it is often necessary to apply several hundred tools including milling tools with lengths of up to 900 mm as well as 60 machining programs or more,” reports Gaylord Klammt.
A true Präwest masterpiece is, among others, a one-of-its-kind shrouded impeller made of stainless steel that has an external diameter of 1,780 mm (70 inch), thus breaking the mold of common dimensioning. Or the extra-large shrouded impeller with solid blade, which stuns even experienced industry experts due to its size of 1.50 m.
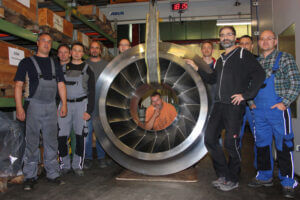
Example of Präwest’s extraordinary manufacturing expertise: Shrouded impeller with an outside diameter of 1780 mm (70 inches)
Stable manufacturing processes are essential
Producing such complex parts with very high quality and simultaneously having a lock on the costs would be impossible without a sophisticated manufacturing strategy. Präwest has already started to optimize all elements of the process chain many years ago. “From our milling strategy to the application of highly precise tools and the right machine tools with powerful controls to perfect CAM programming—we are adjusting all relevant parameters,” says Gaylord Klammt. An error in the production process is a clear no-go here—which is hardly surprising: When the sales price of an individual part can have up to six digits, quality comes first. “Our philosophy is to always be one step ahead of the others—or two steps, even better. And this is only feasible with permanent technical innovation,” summarizes Gaylord Klammt the company’s approach.
Tools are manufactured in-house
The more delicate the processing of a certain material, the more important becomes tool quality. As a consequence, decades ago, Präwest has decided to take tool manufacturing into the company’s own hands and establish an in-house grinding shop. “This empowers us to optimize the tools right at the cutting edge which results in better endurance even when processing superalloys, combined with best surface quality and geometric precision,” states Gaylord Klammt. Plus, the company has learned a lot about the interaction between tool and machine. “We have gained in-depth knowledge about our manufacturing technologies, which makes it easier for us to control every single element,” reveals Gaylord Klammt. Also with respect to cost efficiency, in-house tool production has paid off: It has helped reduce the traditionally high tool-related cost level in the manufacturing of aerospace parts, which are produced in series over a period of five to seven years.
High tech machinery with self-designed 6-axis machines
The large-scale acquisition of top-notch machine tools also contributes to Präwest’s high manufacturing quality: More than 40% of the machines are not older than three years. Last year alone, Präwest invested in ten new milling machines. But that was only the beginning. Despite extensive research, Präwest couldn’t track down a perfect machine tool for the manufacturing of large parts. Hence, the precision manufacturer has decided to develop its own 6-axis milling machines with parallel axes. “These unique machines reflect our manufacturing know-how,” says Gaylord Klammt. “They are better with regard to stiffness, speed, machine volume, installation space, and operator convenience, and they are particularly optimized for milling complex parts such as open and shrouded impellers. They master a product range of 500 to 2500 mm (20 to 98 inches) in diameter and feature dynamic processing for up to 15 metric tons of loading.” The machine tool control comes from HEIDENHAIN.
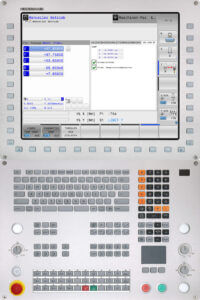
The KinematicsComp feature, here on HEIDENHAIN’s current TNC 640 control
The iTNC 530 impresses all with efficient tool path planning
“We use HEIDENHAIN’s iTNC 530 contouring control,” says Gaylord Klammt. From Präwest’s point of view, this control stands out due to its practically oriented configuration with optimized motion control and jerk limitation, rounding of series of straight-line segments, and contour pre-calculation. “We really like its logic for path planning—or better: for path compensation,” states Gaylord Klammt. “HEIDENHAIN thinks in tolerances, not in functions. The setting options are designed in a straightforward way, helping us simultaneously push the envelope of contour accuracy and traverse speed in programming. This includes the certitude that adjustments of one particular setting will not have side effects on other elements. This approach corresponds to our very own understanding of efficient process optimization.”
Präwest is also very pleased with the control manufacturer’s service. “Functionality is only one side of the coin. The best control isn’t worth a bean if in the end you’re left struggling on your own. Thanks to HEIDENHAIN’s support, we managed to get maximum contour accuracy and speed out of our milling machines,” summarizes Gaylord Klammt.
Milling in different sectors led to mismatch
Although Präwest’s 6-axis milling machines were constructed in the best possible way, their geometrical accuracy did not yet meet Präwest’s high demands. The milling experts detected systematic geometry errors of the linear axes and rotary axes. These errors may be acceptable on small machine tools with wide manufacturing tolerances, but they are causing trouble on large machines with parallel axis that are supposed to produce high-precision parts: Systematic errors from different sources add up to an unacceptable total error, on the one hand due to large movements in the six axes, on the other hand due to the immense size of the tools.
“When machining big workpieces, you mill in different sectors and finally meet in the middle. Many parts require reversal and re-clamping during manufacturing, which also leads to imprecision. When mismatch occurs, our staff has to rework the part or adjust the programming—and that costs money and time,” emphasizes Gaylord Klammt. Because of small batches and expensive materials, Präwest cannot allow test running the NC programs. “Consequently, the question was: How do I manage to produce a dimensionally accurate part in six axes of movement when the part is more than two meters long and the accuracy tolerance is only ± 0.05 mm (±0.002 inch)?”, explains Gaylord Klammt.
Measurement system LaserTracer-NG calculates compensation values along all movement axes and transfers them to the control software
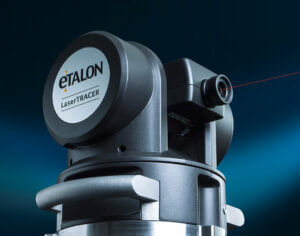
Was specially designed to increase the accuracy of machine tools and coordinate measuring machines: LaserTracer-NG from Etalon
The measurement equipment manufacturer Etalon provided the answer: The German company has developed a self-tracking laser interferometer specially dedicated to increasing the accuracy of machine tools by means of volumetric compensation. With Etalon’s technology, it is possible to calculate exact compensation values for spatial errors in all degrees of freedom. With micrometer accuracy, the system analyzes position errors, straightness errors, rotation errors (pitch, yaw and roll), and squareness between the axes in the whole working volume of the machine tool. Angular positioning deviations, axial and radial movements, and wobbling of the rotational axes are comprehensively recorded as well. Thus, the LaserTracer-NG fundamentally differs from conventional laser interferometers that involve elaborate aligning and generate a large amount of work for determining pitch, yaw and roll.
After measurement data acquisition, Etalon’s software calculates the volumetric compensation data. Because it is interfaced with the machine controller, this data gets automatically transferred to the machine.
KinematicsComp corrects the kinematic description of the machine tool
To assure the smooth processing of the compensation data, Etalon works closely with the controller manufacturers. “The software option KinematicsComp, which is available for the HEIDENHAIN TNC 640 and iTNC 530 controls, makes it possible to store a detailed description of the machine errors in the control. Subsequently, KinematicsComp automatically compensates the position errors that result from static errors of the physical axes. It considers the positions of all rotary and linear axes as well as the current tool length,” explains Gero Günther from the control manufacturer HEIDENHAIN. “This procedure increases the precision of the tool center point in the whole working space.”
Measurement is a “true breakthrough”
To experience the performance of the LaserTracer-NG in connection with KinematicsComp first hand, Gaylord Klammt invited both Etalon and HEIDENHAIN to conduct test measurements. “I admit: I made Etalon measure the geometrically poorest machine. I wanted to see what kind of results the LaserTracer-NG would produce when being confronted with such highly unsatisfying kinematics. And if an investment in this measurement system would really pay off,” discloses Gaylord Klammt.
In the end, the Präwest team was more than impressed by the results. “Suddenly, this milling machine started to produce with geometrical perfection. Furthermore, we were able to understand the weak points of the machine. A true breakthrough with respect to manufacturing quality, contour accuracy, and process reliability! After the test measurement, we quickly decided to acquire a LaserTracer-NG system plus KinematicsComp.”
Requirements for successful volumetric compensation
Volumetric compensation is not a universal remedy appropriate for any machine: “This method does not release machine manufacturers from the obligation to optimize mechanics,” highlight HEIDENHAIN experts. “Several fundamental requirements have to be met to make sure that volumetric compensation is effective on a machine.”
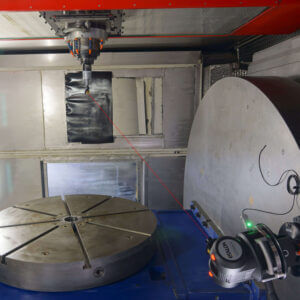
ISO verification with LaserTracer-NG: The measurement process does not require fine alignment of the measurement system.
Measurement process suitable for workshops
The LaserTracer-NG is a high resolution interferometer that automatically follows a reflector continuously measuring the distance to it. The system features an unprecedented accuracy of the center of rotation, which is realized by means of a reflective sphere with a form uncertainty of less than 0.1 μm. The patented beam guide makes sure that this sphere can serve as reference for the interferometric displacement measurement which is therefore conducted with highest dimensional precision to the tool center point (TCP). Consequently, mechanical deviations of the rotation and swivel axes are also acquired with very high precision. Measuring uncertainty for spatial displacement (95%) amounts to 0.2 µm + 0.3 µm/m.
Although this method may appear complex at first sight: The LaserTracer-NG is ready for shop-floor application, and the user is guided through all steps in the software. “Of course you have to learn how to apply the system,” says Stephan Kunath, head of industrial machine tooling at Präwest. “However, Etalon’s team provided great training and is always within easy reach in case of questions. I’m very happy with the handling of the measurement system. Today, the measurements are well-established routines for me. I can do the whole compensation of a large 6-axis machine on my own in a short time.”
For conducting the measurement, Stephan Kunath places the compact LaserTracer-NG in the machine volume several times without any particular fine-alignment. Instead of a tool, the reflector is clamped in the spindle. Then, the measurement system is ready to start the automated measurement process: It tracks the actual path of the machine in its entire working space. The required NC programs are automatically generated by Etalon’s software, and the respective distances to the tool center point are determined interferometrically. Etalon’s system transfers the recorded measured data to the connected Trac-Cal measuring software, which automatically analyses the measured data and transfers the volumetric compensation values to HEIDENHAIN’s iTNC 530 controller via KinematicsComp.
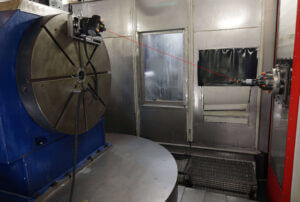
Rotation axis calibration of a large machine tool with axes travels of 2.5 x 2.3 x 0.8 m³. The LaserTracer-NG—mounted on a rotary table with a diameter of 1.2 m—is positioned stationary in the machine several times.
Volumetric compensation done on demand
Not only does Präwest volumetric perform compensation in pre-defined intervals, but also—and mainly—on demand. “Whenever we notice errors in preliminary stages of production that cannot result from any other processes, we decide to conduct volumetric compensation,” explains Gaylord Klammt the procedure. “Previously, iterative adjustments used to be part of the process—today, the LaserTracer-NG and KinematicsComp make this superfluous.”
Outlook: Machine accuracy greatly increased
Präwest’s experience has been the following: When volumetric compensation is performed on a milling machine, the geometric accuracy of the workpiece increases significantly, especially when machining complex parts. “We are speaking about dimensions that would never have been possible with other methods,” sums up Gaylord Klammt. The improved machining accuracy comes with perfect timing as Präwest is planning to enter a new business area: prototype manufacturing for the aerospace industry. “Our customers long for ultra-high precision. At the same time, we want to keep up our profitability. Thanks to volumetric compensation, we are in the position to realize maximum quality in production with manageable effort—even with extremely tight geometric tolerances. The technology helps us to reliably uphold our reputation as precision manufacturer.”