March 23, 2022
One micro step for M5, one giant leap for healthcare
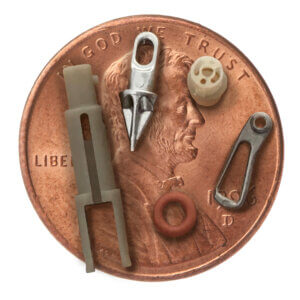
Five parts with complex geometries shown atop a penny made at M5. These parts are made of varying material including PEEK, rubber and Cobalt Chrome.
Investing in new 5-axis machine tools for micro-machining and meeting the needs of critical medical device manufacturers during the COVID-19 crisis pays off for a small job shop in Minnesota. Supported by HEIDENHAIN controls on KERN machine tools, M5 has been able to play an important role in the movement to wellness so desperately needed during a pandemic.
When a medical device manufacturer needed an extremely detailed micro-fluidics mold part that included approximately 30 channels required to facilitate making essential vaccines and other drug therapies during the COVID-19 pandemic, who expected a small job shop in Minnesota to get the job? Jon Baklund, the owner of M5, that’s who.
“In early 2020, we decided to take a risk to grow our already established micro-machining capabilities by purchasing a new 5-axis machine tool specializing in such,” explained Baklund. “Soon after implemented, we bought a second. Two of the best investment decisions we’ve ever made.”
With a rush to mobilize resources to combat the global COVID-19 pandemic that boldly reared its ugly head in the U.S. in early 2020, M5 became a critical vendor. With a staff of four and a machine shop of about 20 machines doing specialized micro-machining production, M5 is meeting the needs of many essential medical equipment businesses and others.
M5 (Minnesota Micro Molding, Machining & Manufacturing) based outside of Minneapolis has grown from a tool and die shop to a strong and reliable source for small parts (almost always less than the size of a hand) and micro-machining/molding. “The part sizes requested kept getting smaller over time so in early 2020 we further pushed our resources in that direction and obtained our first KERN Micro Vario machine tool equipped with a HEIDENHAIN TNC 640 control for 5-axis micro-machining,” explained Baklund. “Not only did this add an innumerable amount of new capabilities and capacity, but it also brought in new customers. In fact, with it, we have been able to push the limits further on accuracies that we would have never even contemplated attaining before, attaining the very highest and tightest tolerances and surface finishes that we’ve ever had. And when I talk about capabilities, I am referencing the fact that these machines are full dynamic 5-axis machining centers, with high-speed spindles up to 42,000 rpm!”
The Micro Jobs
The silicone mold part for pharmaceuticals that Baklund mentioned above, for example, has approximately thirty .010” wide channels. M5 staff had to machine the entire bottom of the mold with a single .008” diameter end-mill as to be held to a near perfect flat surface so that it would not have any steps or individual facets in it. It took 22 hours to get that first exacting surface using 5-axis machining. Now completed, it can be used to make plates that allow varying liquid medication/materials to go into the channels, then blend to make varying drug therapies/vaccines. For this project, M5 made eight of these microfluidic molds in 2020 at the very high accuracies required by the customer. “Having a machine like the KERN Micro Vario with the HEIDENHAIN control gave us great control over spindle growth, especially when 50 millionths matters!” added Baklund.
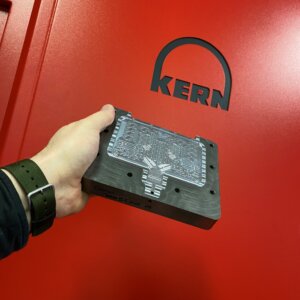
M5 made this microfluidics mold with .010” wide channels. The entire bottom of the mold was machined with a .008 diameter end mill as to be held to a near perfect flat surface. These molds are used to make a product that is utilized in formulating drug therapies such as vaccines.
“Our production at M5 is generally under 500, and we do a lot of prototyping of tiny parts, assemblies and fixtures for customers with incredibly high accuracies,” said Baklund. Alex Madsen, (part owner) lead tool maker and designer, added “In fact, in 2020, utilizing Zoom, we had many conversations with customers about their needs asking ‘what is your hardest or most unusual part that you’ve been trying to make or have made, but can’t?’ Then we offer to make it, and successfully do! “The two things we are most proud of here at M5 is the high part quality and quick turnaround.”
The acquisition of the 5-axis machine tool has allowed M5 to handle many much-needed medical equipment parts jobs quickly, and word has spread. Many jobs during the pandemic were done around the clock using the HEIDENHAIN TNC 640 controls’ remote desktop manager to work at night from home. Four months after starting up the machine tool, a second KERN/HEIDENHAIN was added to the shop. Its small footprint allowed easy implementation.
Toni Mangold, the President of KERN Precision, even commented: “I have a feeling that many working in commodities manufacturing had a very hard time getting through the pandemic, but M5 was able to set themselves apart and meet an important need. Especially apparent during the COVID crisis, we are all realizing how important exacting manufacturing technologies are to the human condition.”
Another recent example of medical equipment parts completed quickly by M5 with their newly acquired machine tools includes critical components for a one-trigger, Inneurco device used in brain surgery on stroke victims. This small device is developed to be able to quickly penetrate a brain blockage, cut and suture at one pass. M5 expediently handled the micro-machining/molding/welding of multiple important parts for them. “By doing this, we were happy to enable our customer to get their product to market faster,” said Baklund.
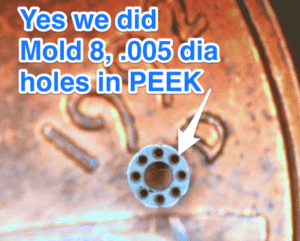
M5 manufactured this tiny hub to be used in a pacemaker. Here .004” diameter size wires will run through a .005” diameter a hole.
M5 also was responsible for micro-molding tiny prototype components on their patented Desktop Micro Molding Platform for a Medtronics part for pacemakers where tiny wires will be run through before implantation in a human heart. “Here .004”-size wires will run through eight .005” diameter holes,” explained Baklund. “And the parts cannot be touched by human hands in order to keep it sterile, hence the importance of this mechanical automation and the need for these super high accuracy machines.”
Baklund also pointed out that not just any machine tool can do this type of delicate work as thermal expansion can cause machining issues when dealing at these microlevels. He noted that his new machine tools are easily controllable and liquid-cooled throughout to eliminate that. “For years we worked at getting our micro process refined,” said Baklund. “As those at other manufacturing companies will understand, we work through issues on many machine tools. This is why we ended up adding the HEIDENHAIN-controlled KERNs. They just get the job done and don’t need to be in a temperature-controlled room.” Mangold confirmed that this KERN machine is configured with pumping cold water throughout the structure, making it more temperature-stable than its outside environment.
“This often results in a HUGE cost savings for manufacturers who no longer need to acquire giant AC units and more to stabilize their rooms,” Mangold added. Baklund added, “Not only does it result in cost savings, which is certainly a consideration, it also gives us the ability to do much more critical processes and achieve finer surface finishes which brings profitability.”
Critical Machines
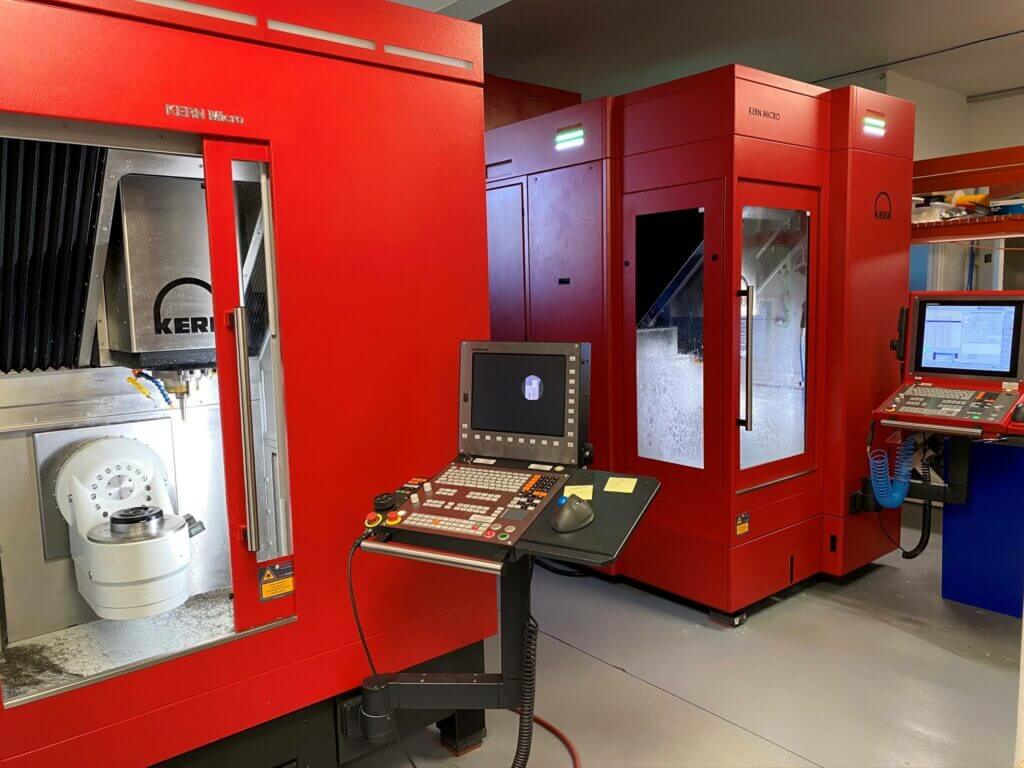
The two KERN Micro Vario machine tools with the HEIDENHAIN TNC 640 controls were critical tools at M5 during the pandemic.
Working in the micron range, accuracy is of the utmost importance to M5. The penny shown above sits under five parts micro-molded at M5. “We spent a year and a half researching 5-axis machine tools for our shop,” said Baklund. “And I’m more than happy with our decision. I believe the KERN with the HEIDENHAIN control is the most accurate 5-axis machine tool on the planet! I’d put it up against anything! They allow us to build our precision micro-molds to a level we have not been able to in the past.”
Madsen, who has 11 years at M5, concurred “I love them! I’m regularly using end mills of .003” diameter on hardened steels with these machines, often resulting in surface finishes like mirrors. Also, the 5th axis really helps with tool life. Being able to machine five sides of a part at one time eliminates having to fixture second clamping.” With no prior experience with 5-axis machining or a HEIDENHAIN control, Madsen was up and running in a week and a half from receiving the first Micro Vario. Right from the start, Madsen was doing very complex operations and already completing jobs to go out the door.
“You know the first thing I noticed about the HEIDENHAIN control was that it uses a more verbal language as far as for tool changes and things like that,” explained Madsen who has been using Fanuc controls most often for years. “I wish every machine in our shop was a HEIDENHAIN control! The learning curve is short and self-explanatory, and much more intuitive. Even if I am manually typing in some G-code, the programming screen provides a description as to what it is and what I should look for. And the tool table is nice, as well as the probing cycles are super easy to follow.”
KERN’s Mangold added “it’s super important to us to have a control that can handle the latest advanced technology that is built into these Micro Varios. We standardize with HEIDENHAIN controls because of their high level of built-in technology that enable our machines to reach their full capability and for the user to do great manufacturing quickly and easily. There are all these unique technologies built-in to this machine and the user doesn’t need a PhD to run it. You simply use the cycles on the control, and it works!”
Madsen added “I’ve also found that the HEIDENHAIN TNC simulation test run screen is extremely accurate. I basically do a full render of my part on the control, and there have been times where it shows a half a thousandth step off that was found in the G-code and the HEIDENHAIN control shows it! So, on these really tiny parts where I need super-fine surface finishes, I can prove it out on the control, and I trust what I see. And it turns out as expected!”
One of the favorite TNC optional control features that Madsen uses is Dynamic Collision Monitoring. Baklund explained that they leave it turned on at M5. “It is worth it because if you crash a spindle, the cost could be $60,000!”
Madsen explained that this is important to him since he is sometimes doing five or six different types of parts a day between two machines running simultaneously. And that he needs to trust that he can walk away from a setup to view another. “This allows me to be more efficient and productive. I rely on the Collision Monitoring every day.”
Summary
Approximately 80% of M5’s work during the pandemic has been in serving medical equipment companies, though other industries included aerospace, micro-electronics, computer assembly, and semiconductor. Through it all, and with the KERN/HEIDENHAIN machine tool investment, their business did well.
“You know, M5’s addition of these two machine tools really allowed them to implement automation simply and quickly in their small shop,” added Mangold, “running daily unmanned night shifts, with no expensive robots required.
“And these machines were able to produce the necessary parts in tolerance, at the same time allowing enough margin so that they didn’t need to measure every single part. This produced huge benefits for them.”
M5 has much to look forward to in the days, months and even years ahead. “When you combine the accuracy of a machine like the KERN Micro Vario with the control capabilities of the HEIDENHAIN TNC 640, the number of new possibilities that open up to a company like ours is virtually endless.”
Mangold added “I think that since the start of the pandemic, more people have come to realize the importance of manufacturing technology to our world, especially during a crisis. M5 and others like them can and are truly making a difference.”
The HEIDENHAIN Group also supports Life Sciences with products from daughter companies IMT and ETEL specializing in non-glass applications.