March 19, 2019
Patient comfort and Functional Safety
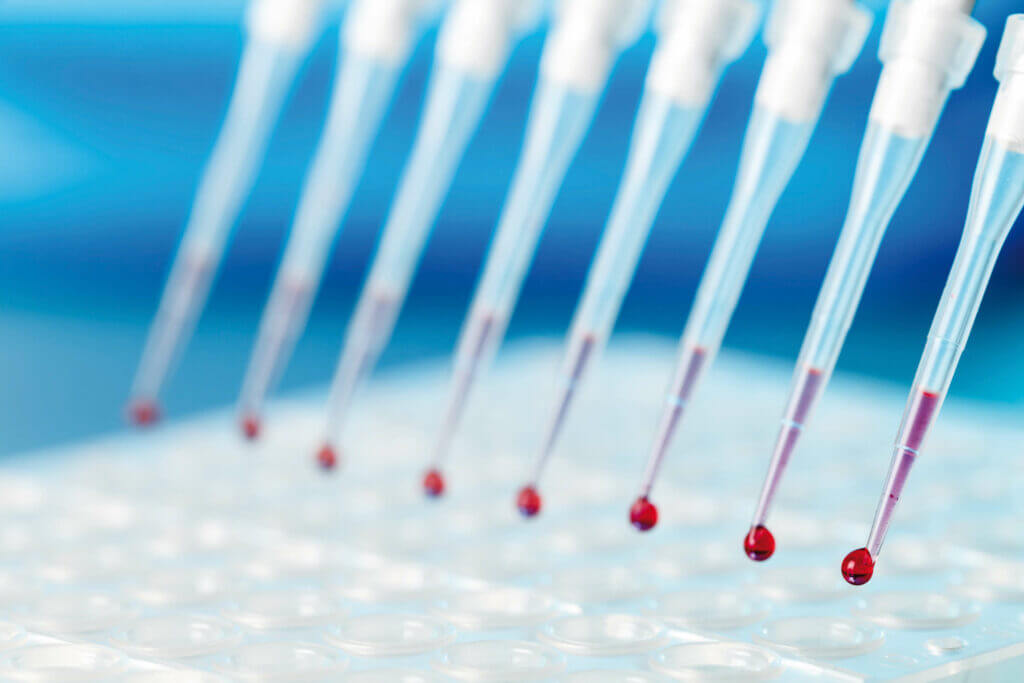
The transfer of samples without losses in highly automated laboratory equipment, such as in automated pipettors, is made possible through exact positioning and smooth control behavior for jerk-free traversing movements.
Reliable Position Measurement with HEIDENHAIN Encoders in the Medical Technology Industry
In a variety of ways, the medical technology industry is both extremely demanding and highly multifaceted. With the LIC 2100 exposed linear encoder along with the ECN 1123 and EQN 1135 rotary encoders, HEIDENHAIN offers reliable, highly accurate solutions for applications such as patient positioning or position measurement in automated laboratories.
At first glance, patient positioning and laboratory automation appear to be two completely different fields within the vast medical technology sector. Yet, precisely when it comes to positioning, they share many commonalities: both of these applications require encoders featuring high position accuracy, absolute measurement without backlash, high reliability, failure safety, ruggedness, and a compact design. The LIC 2100 exposed linear encoder as well as the ECN 1123 and EQN 1135 rotary encoders from HEIDENHAIN fulfill exactly these requirements.
Encoders for exceptional patient comfort and high-accuracy imaging
When the examination table of a modern CT or MRI machine is moved for positioning, motion must be measured and controlled in a variety of directions. In order for the patient to reach the table, for example, the table’s height can be adjusted. Then, with the patient lying on the table, it is moved into the scanning area. In both of these operations, patient comfort is paramount. Smooth, gentle motions make the patient feel safe and prevent causing pain.
Once in the scanning area of the diagnostic machine, the patient, or rather the part of the body to be examined, must be brought into exact position before the examination can begin. In addition to longitudinal and transverse positioning, the inclination is adjusted as well. Then, depending on the diagnostic procedure, the patient must be moved through the scanning area in a controlled manner with exceptional precision so that images with the desired slice thickness and required resolution can be generated.

The HEIDENHAIN LIC 2100: The exposed linear encoder with absolute position measurement ensures smooth motion, providing comfort to patients during positioning as well as advantages for liquid handling in the lab.
The LIC 2100 exposed linear encoder along with the ECN 1123 and EQN 1135 rotary encoders are extremely well suited for these applications. By directly measuring the absolute position at all times without a reference run and by transmitting high-resolution position values, these encoders permit highly dynamic closed-loop control of the drives. Acceleration and deceleration are, in turn, barely perceptible, resulting in very smooth and comfortable movements for the patient. At the same time, positioning is also highly accurate.
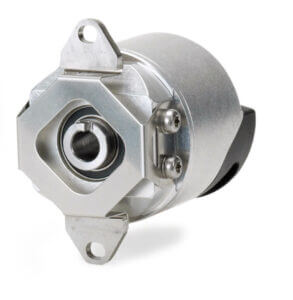
The ECN 1123 and EQN 1135 rotary encoder versions with functional safety ensure high availability for medical technology equipment.
As encoders with functional safety, the ECN 1123 and EQN 1135 also provide a high degree of self-monitoring and self-diagnostics. They thus deliver data for the preventive management of servicing and maintenance intervals. Moreover, the HEIDENHAIN EnDat 2.2 interface permits online diagnostics of the encoders’ operating status so as to enable high availability of the expensive diagnostic imaging equipment. A mechanical fault exclusion feature aids in this as well.
Error-free transfer of samples in highly automated laboratories
Modern medical laboratories are characterized by heavily automated processes with high repeatability. These labs are tasked with analyzing tiny individual samples in large batches within a very short amount of time. This is why, for example, the wells on microtiter plates are becoming ever smaller and more closely spaced. By this means, large sample batches can be analyzed with only a tiny amount of expensive reagents.
In order for the analysis results to be absolutely reliable and correct, laboratory equipment, such as automated pipettors for liquid handling, must be controlled with great precision. One faulty transfer of liquids could lead to erroneous results and the destruction of valuable and possibly irreplaceable samples. The fact that many devices are equipped with redundant measuring technology that continuously monitors the position shows just how important accuracy is in modern laboratory technology.
The LIC 2100 absolute linear encoders from HEIDENHAIN ensure high positioning accuracy at rapid traversing speeds in automated labs as well. The absolute measuring method of the encoders provides exact information at all times regarding the position of the pipettes in a pipettor, for example, while eliminating the need for system referencing. The high resolution of the encoders and the rapid transfer of data to and from the control over the EnDat serial interface permit highly accurate positioning while also ensuring exceptionally smooth and steady control behavior for jerk-free movement of the samples.
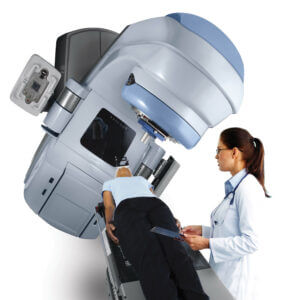
Thanks to exceptionally accurate linear and rotary encoders from HEIDENHAIN, modern CT and MRI machines ensure a high level of patient comfort and exceptional image quality (image used with kind permission from Varian Medical Systems, Inc., all rights reserved).
For patient positioning or lab automation: LIC 2100 exposed linear encoder
Thanks to its high reliability as well as its accuracy grade (±15 µm/m), the LIC 2100 exposed linear encoder is ideal for patient positioning or for applications in lab automation. As an absolute encoder, the LIC 2100 always provides accurate position values directly after equipment switch-on without the need for a reference run. Its measuring standard, which is resistant to contamination and wear, lends the LIC 2100 its high process reliability. In addition, the encoder’s scanning head attains an IP67 rating, thereby meeting exceptionally high demands for protection against dust and moisture for long-term, reliable operation. Measuring lengths of up to 3020 mm are available in the standard version, with specialized customer-specific solutions of up to 6020 mm possible as well. Thus, even long control and measurement distances in linked laboratory lines can be monitored and controlled with high accuracy.
But these are not the only characteristics that make the LIC 2100 such an attractive solution for manufacturers of medical technology equipment. Its ease of installation, with extraordinarily wide mounting tolerances, is yet another argument in favor of this exposed linear encoder from HEIDENHAIN. A variance of up to one millimeter is permitted for the gap between the scanning unit and the scale tape (adhesive mounting: 0.75 mm ±0.5 mm; mounting with aluminum carrier: 0.75 mm +0.5 mm/–0.25 mm), with ±1 mm of lateral offset also allowed. In two axes of motion, the scanning unit can be misaligned relative to the scale tape by up to ±1 degree for each axis (roll and pitch). Maximum permissible yaw is ±2 degrees. These tolerances present no hindrance to measuring accuracy or the high maximum traversing speed of 600 m/min.
The installation of the scale tape, with either a scale tape carrier made of aluminum or by means of direct adhesion, saves time and effort during equipment manufacturing. A wide selection of serial interfaces, including of course EnDat 2.2, rounds off the list of installation advantages with the encoder’s ease of electronic connection.
For safety-related applications: ECN 1123 and EQN 1135 absolute rotary encoders from HEIDENHAIN with mechanical fault exclusion
The ECN 1123 and EQN 1135 absolute rotary encoder versions with functional safety were designed by HEIDENHAIN specifically for safety-related applications in the medical technology industry. These encoders are certified for safety-related applications in conformity with SIL 2 (EN 61508) or Category 3, Performance Level d (EN ISO 13849). They also feature mechanical fault exclusion. Their positive-locking hollow shaft features a special positive locking element that securely locks into a corresponding groove in the drive shaft during the mounting process and very effectively prevents slippage in the shaft connection.
Both rotary encoders provide absolute position values: the ECN 1123 with a singleturn resolution of 23 bits, and the EQN 1135 with an additional multiturn resolution of 12 bits. Data is transferred over the purely serial, bidirectional EnDat 2.2 interface. In their functional safety versions, the rotary encoders provide two independently generated position values over this EnDat interface. The PFHD value, which represents the probability of dangerous failure per hour and is required for the evaluation of safety systems, lies below 15 x 10–9 for these rotary encoders.
Thanks to a housing diameter of only 35 mm, the ECN 1123 and EQN 1135 rotary encoders are particularly well-suited for applications with low installation space, such as on small servo motors with a flange size of 40 mm, as are common in the medical technology industry. Also fitting for this type of application and integrated into the encoders’ electronics is the capability of evaluating a temperature sensor in the motor winding. The EnDat protocol transmits the digitized temperature value purely serially, thereby reducing the number of wires in the cable by two.