February 9, 2023
Q&A with Milton Willis: The new EnDat 3 interface
We recently sat down with Milton Willis, our Machine Tool Product Specialist, to talk about our new EnDat 3 interface. In addition to covering highlights of the newest generation, we took a look back at the history of EnDat, and what sets it apart from other encoder interfaces—particularly in the Machine tool and Automation category.
Can you give a brief history of the EnDat interface?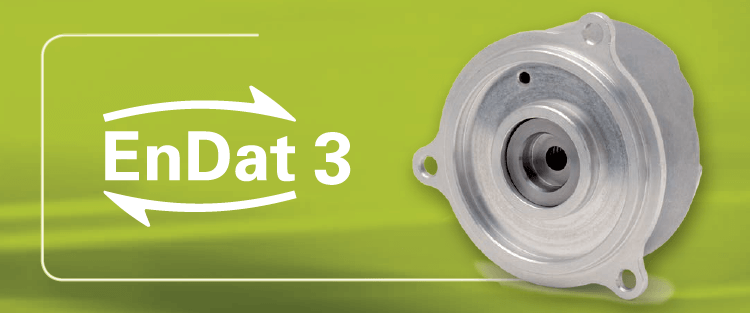
EnDat is an absolute position encoder interface. EnDat 2.1 was created in 1995, and at that time it was developed to solve a challenge. Most encoders at the time utilized technologies that were analog or digital incremental interfaces. So, we created EnDat with an RS-485 output signal, which is more robust and less susceptible to noise. We knew this was very important to Machine Tool manufacturers (as well as Automation and other Electronics OEMs) and their end users—because HEIDENHAIN has always been entrenched in this industry. This encoder interface was developed largely with them in mind.
So what are the specific benefits of the EnDat interface for the Machine Tool market?
One major benefit of a machine tool that features the EnDat encoder interface is that when the machine starts up for the first time, users don’t have to home or reference the machine to a specific location to establish a starting point. The CNC automatically reads the position data from the encoder without any machine movement. Imagine a 100-foot-long machine having to home /reference to one location. That can be very time-consuming for the user. With EnDat, the user can establish a starting point anywhere on the machine without ever having to move the machine. The benefit of that is quicker startup, which equates to faster cycle times and more throughput for the end user.
Secondly, the bi-directional EnDat 2.2 interface enables the support of monitoring and diagnostic functions both before and during machine tool operations. Through preventative maintenance (with many Endat 2.2 encoders) the user can read the diagnostic values from our encoder. Also, during machine operation, if a fault is detected an error is sent to the CNC and the end user is warned. This ensures reliable and precise positioning data which is an important attribute for today’s highly accurate CNC machines.
Finally, EnDat 2.2 offers extended power supply range (3.6 -14VDC). Today’s CNC machines are larger and use very long cables, up to 150 meters. Having such a wide voltage operation range reduces faults that will occur due to voltage drop. Our supply voltage requirement also simplifies encoder integration for our Machine Tool OEM’s.
How does EnDat support next-gen Automation—both in the Machine Tool space and beyond, with robotics?
Functional safety is a big thing in Automation. The European market is already very stringent with this, but the U.S. and other markets are catching up. EnDat makes compliance easier because we offer pre-certified EnDat Functional Safety encoders with capability up to SIL 3 PLe.
What are the new features and benefits of EnDat 3?
Simply put, the new EnDat 3 interface has all the benefits of its predecessors, but it is even faster and more robust. We went from a 16 to 200-kilohertz clock frequency as well as from a 12.5 to a 25-megabit bandwidth. So, it allows for the transfer of information much more quickly. In EnDat 3 we have also simplified the functional safety aspect. EnDat 3 now leverages the industry standard for functional safety; black channel. This makes implementation much easier on the OEM.
We also have reduced the cabling in the EnDat 3, going down to a two or four-wire setup. This is a big benefit in the Machine Tool and Robotics sector. And for Robotics applications, the new EnDat 3 offers bus operation, which allows manufacturers to daisy-chain encoders together, which can also reduce cabling. This not only simplifies design and manufacturing, but it’s also a cost savings for the manufacturer because they cut down on wire and cable.
In terms of more robustness, the EnDat 3 has more memory and storage capacity. One example is that we went from the capacity for 2-space DATA packets to 15-space DATA packets. Another function that benefits the end user is the ability to password-protect information that is stored in the encoder. For example, specific code or machine information to which the company or manager might not want to allow full access.
Another example relates to new encoder technology Multi-DOF encoders (Measurement Technology for Multiple Degrees of Freedom). Multi-dimensional encoders support was added allowing easier installation and simplifies the downstream calculation that’s involved with using multiple reader heads with the use on a single cable.
Finally, with EnDat 3, we have expanded the number of temperature sensors with which to monitor everything from the temperature of a robotics arm to the temperature inside of a cabinet.
We say that EnDat 3 is “future-ready”. How so?
In addition to the increase in frequency and bandwidth, we’re always aware of designing the interface so that it supports the latest technology, demands and encoder types. EnDat 3 gives us the ability to relieve the load on high-level motion and safety controllers. The functional safety aspect that we mentioned is one. As the demands here become greater in the future, this interface will support future development.
- Decreased cycle time (Bus Operation)
- Added support for additional sensors
- Operating status acquisition
- Transmission of additional position data for Multi-DOF encoders