October 17, 2018
How semiconductor producers are keeping up
Historically, few components, of any kind, require the level of production precision of semiconductor components. Considering the increasing variation in mobility and environmental influences on their performance and physical obsolescence—think artificial intelligence, autonomous vehicles, the internet of things, 5G communications, the list goes on—limits are being pushed even further.
Add the fact that application and adoption of these technologies is far from mature, and the accelerated growth is sure to continue; global sales are now in the ballpark of $500 billion. Staggering.
This begs the question, can semiconductor producers keep up? Can they satisfy more complex, demanding applications and increasing market demand at the same time? The short answer is yes, but not without the development of some spectacular technologies and processes.
Advancing integration and increasing external contacts
There have been significant advances in packaging of components that are used in the aforementioned applications. When compared to standard wafer-level packages, the relatively new approach of fan-out wafer level packaging allows for higher input/output, a smaller footprint and improved thermal and electrical performance.
Needless to say, the production process is a complex one, involving a reconstitution of the wafer with dies embedded with low-cost materials that help make the use of high-cost silicon more efficient. These add precise fabrication steps, but as we’ve established, producers can’t afford dramatic slowdowns. So, how are they doing it?
They’re using a combination of powerful hardware and software—like HEIDENHAIN absolute encoders and ETEL motion stage technology with nanometer-level stability paired with a high-speed, serial interface like our EnDat. This kind of assembly provides absolute positioning with single nanometer resolutions at ultra-fast speeds, exactly what today’s semiconductor producers need.
Added complexities require closer inspection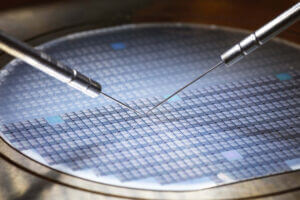
Advances like fan-out wafer level packaging introduce variables to the production process and, in turn, a higher chance for imperfections in the end product. This too requires extreme speed and accuracy for efficient, profitable semiconductor manufacturing. Two specific solutions are proving invaluable in this process.
First are ETEL controls that can calculate the best path-performance for inspection and placement tools using algorithms—similar to those used to help race car drivers turn corners at high speeds. Second is the HEIDENHAIN LIP 6000 encoder; it’s necessarily small and has a signal stability of 0.4 nanometers at 1 MHz that gives a motion system millisecond-level seek and settle times.
Dicing with care
Dicing is one of the final steps in the semiconductor fabrication process, making the stakes extremely high. Errors separating the dies within the wafer can be extremely costly considering the modern processing required to get a semiconductor chip to this stage. Regardless of method, saws or something more high-tech, smooth and accurate motion is paramount for the dicing tool.
A custom ASIC HEIDENHAIN just introduced called HSP 1.0 (HEIDENHAIN Signal Processing) used in encoder reader heads is ideal for dicing. HSP 1.0 amplifies the LED intensity as the encoder moves and learns about contamination that may be on the scale. ETEL has also introduced QuiET, a proprietary active isolation module that supports the entire motion stage by eliminating incoming vibrations and counteracting stage motion for stable, high-resolution performance, helping the semiconductor industry reduce street widths and deliver finished products on time.
The semiconductor industry is in the midst of a boom. In order to keep the momentum, advanced encoder and motion stage technology will be necessary to execute more difficult processes on time and in bulk. Accuracy, speed and reliability will continue to be absolute must haves, and that’s exactly where HEIDENHAIN and ETEL excel.