Optimize machine accuracy
The growing need for higher machining tolerances is placing ever greater demands on machine tool accuracy. Machining results such as tolerance compliance and surface quality are largely determined by the dynamic and static accuracy of the machine’s movements. But due to imperfections arising from production and installation, machine tool components exhibit elastic deformation.
That’s why any kind of precision work requires measuring any motion errors and compensating for them as needed. HEIDENHAIN offers several ways for you to improve the quality of your machine.
Dynamic Precision: high dynamic performance and accuracy
The Dynamic Precision functions are available as stand-alone or combinable options for HEIDENHAIN controls.
- CTC: greater accuracy through compensation of acceleration-related position errors at the tool center point
- AVD: superior surfaces through active vibration damping
- PAC: position-based adaptation of control parameters
- LAC: higher accuracy through load-based adaptation of control parameters, regardless of the load or machine age
- MAC: motion-based adaptation of control parameters
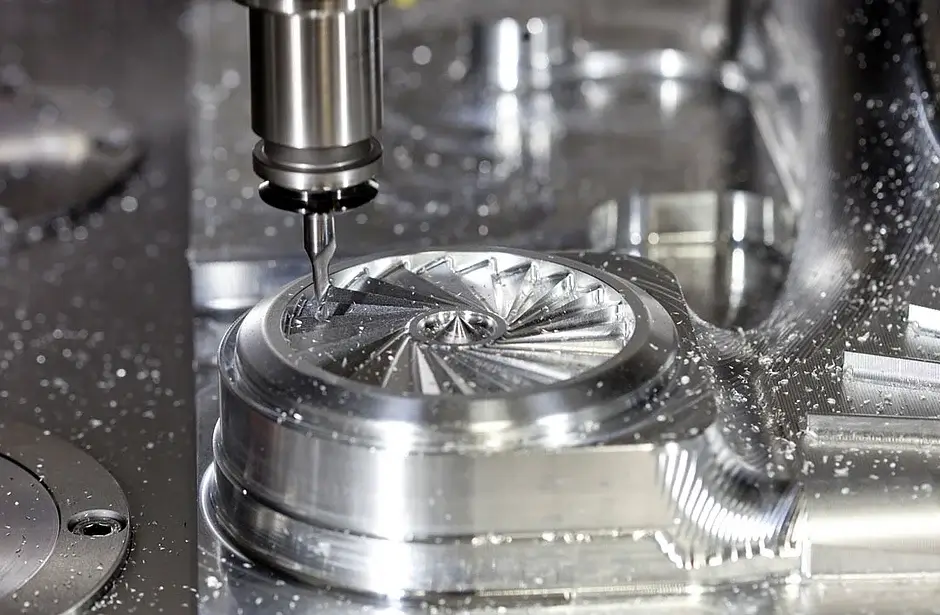
KinematicsOpt
This option is a cycle firmly integrated into the TNC, enabling the fast and easy inspection and optimization of the machine’s kinematics. And although it cannot compensate for statistical machine errors on its own, it can help find them.
KinematicsComp
KinematicsComp can significantly increase machining accuracy and contour precision. On large machines, the long traversing paths and high workpiece weights cause relatively high errors. Because reducing them at a mechanical level is very difficult, KinematicsComp provides clear economic benefits. It also achieves improvements on small machines with high accuracy requirements.
Volumetric compensation
Volumetric compensation is used to determine the volumetric error in the entire work envelope on new and used machine tools with a HEIDENHAIN control. Various measuring methods are available depending on the requirements. In one such method, an error model with compensation files is created based on multiple point measurements made with a laser tracer from various positions. As a result, static geometric errors can be reduced, and the TCP position can be improved throughout the volume. These measurements are offered by the HEIDENHAIN Service department.