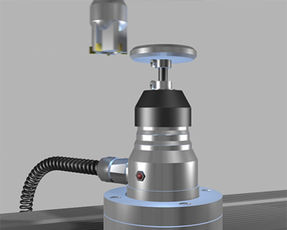
Tools
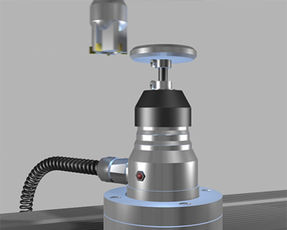
Symbol overview
Symbol | Meaning |
---|---|
Tool carrier reference point T | |
Tool change position B | |
Tool shank point N | |
Tool set point E |
Tool shank point and tool set point
The tool set point E serves as the reference point for the length and radius values determined on the tool presetter.
The control uses the tool shank point N as the origin of the defined length and radius values.
If tool measurement is performed outside the machine, these points at the tool holder and spindle will have an enormous impact on the subsequent machining process. After a tool change, if these points do not coincide, then either too much or too little material will be removed.
Tip
So if possible measure the tools directly in the machine or using a tool presetter that has to be calibrated specifically for each machine.
Tool measurement
- Measurement types:
- By scratching or with a measuring standard in the machine
- By using a tool touch probe or a toolsetter in the machine
- By using a laser touch probe in the machine
- By using a tool presetter outside the machine
Tool touch probe
The TT touch probe is mounted insid the machine. It allows tool measurements directly in the machine.
- Characteristics:
- Measurement by means of direct contact
- Stationary or rotating tool
- Individual or overall cutting edge measurement
- Wear and breakage check
Laser touch probe
The non-contacting TL touch probe is mounted inside the machine. It allows tool measurements directly in the machine.
- Characteristics:
- Contact-free measurement
- Stationary or rotating tool
- Accounting for the spindle by measurement at rated speed
- Individual or overall cutting edge measurement
- Measurement of forming tools
- Creation of compensation value tables, e.g. multiple radius values for a spherical cutter (depends on the inclination angle)
- Wear and breakage check even during the program run
Tip
The laser-type measuring device enables you to also measure very small and fragile tools.
Fixed pocket assignment
In theory, more than 32 000 tools can be defined per control system.
However, since no machine has a magazine of that size, you can assign tool pockets to the tools existing on the machine.
If the machine always returns the tool to the same magazine pocket, this is referred to as a fixed pocket assignment (manual pocket selection).
Flexible pocket assignment
If the machine places the tool in the magazine pocket of the subsequent tool, this is referred to as a flexible pocket assignment.
This variant saves a lot of time when changing tools frequently.
Tip
In order to avoid tool collisions inside the magazine, you can still assign fixed pockets to specific tools. This creates a mixed pocket assignment, which is used e.g. for tools with extra length or width.
Through the assignment of a predefined pocket type, the control automatically recognizes whether the tool is extra long or extra wide.
The milling process
For the various milling processes and machining strategies, different tools, such as roughing or finishing cutters, are required.
- Examples:
- Face milling
- Circular milling
- Helical milling
- Hob milling
- Profile milling
The control supports the definition of different tool types based on corresponding columns in the tool table.